05.2024 Cover Story
Innovation X, Craftsmanship, Low Carbon Production, New Solutions
Far Eastern Magazine / Editorial Room
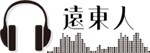
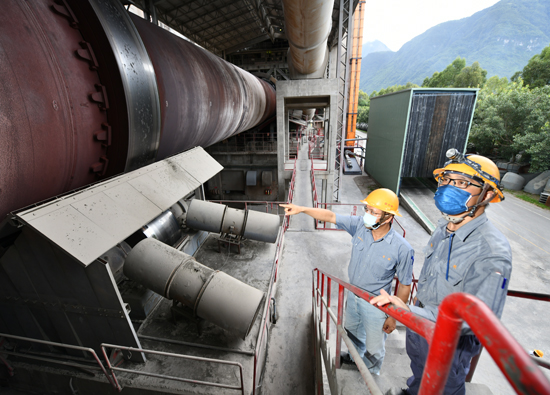
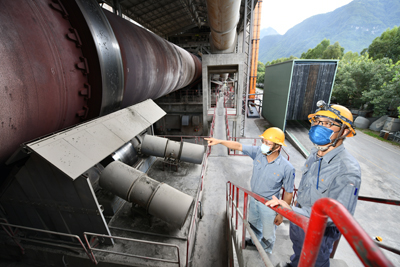
Research and development equipment optimization fuel treatment
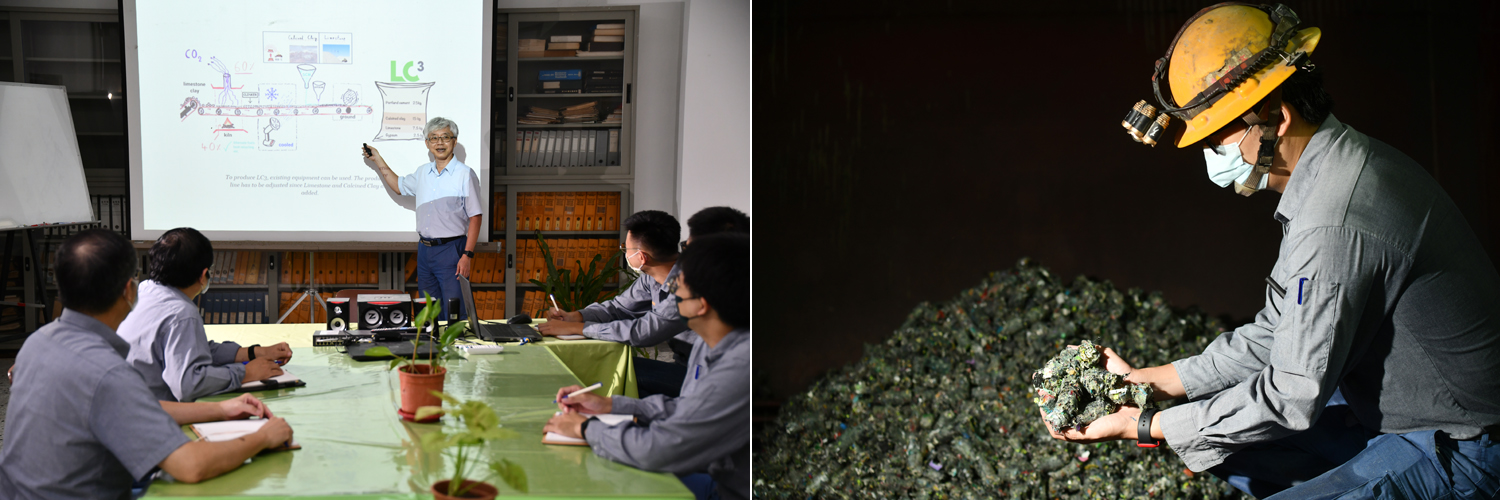
On the other hand, the Russia Ukraine war has led to a surge in global coal prices, and the upcoming carbon bill has also caused a sharp increase in production costs. How to reduce costs has become an urgent challenge for major cement plants.
In order to keep up with the times, Asia Cement Corporation's Hualien plant has been committed to transforming towards a "recycled economy" since 2019. Initially, alternative fuels were loaded into space bags, transported to the 6th floor of the preheater using a mobile crane, and finally added manually by breaking the bags. However, the process requires a significant amount of manpower, material resources, and time, and due to limitations in equipment design, the amount of alternative fuel added still needs to be improved.
After the establishment of alternative fuel transportation equipment in 2021, the feeding was changed to a dedicated feeding port, and then the alternative fuel was sequentially distributed to each kiln using equipment such as screw conveyors, lifting machines, and chain conveyors, successfully improving the feeding efficiency. Taking kiln 2 as an example, the average monthly removal amount is about four times that of manual feeding period. However, due to the inability of alternative fuels to fully burn, increasing the addition amount can easily lead to an increase in carbon monoxide and a decrease in clinker production. Therefore, the removal amount of alternative fuels still faces a bottleneck. At the same time, due to outdated equipment, the dust collection system of the raw material mill in kiln 3 must undergo a 55 day major overhaul, during which it is unable to assist in the removal of alternative fuels, which may result in insufficient stacking space and inability to meet customer needs. It is urgent to improve the use of alternative fuels.
To this end, Asia Cement Corporation Hualien Factory actively sought advice from equipment manufacturers on one hand, and invited the manufacturing, engineering, and electrical and instrumentation teams to brainstorm and ultimately decided to independently install a ramp type combustion furnace in kiln 2 to increase feeding space. A small platform was also planned at the bottom, so that alternative fuels with smaller particle sizes could be directly burned with the rising air duct, while those with larger particle sizes would have longer residence times due to gravity. When the weight became lighter, they would be carried by hot air to the rising air duct for combustion. This would help achieve complete combustion, and a stable heat source would also stabilize the firing process, providing space for kiln operators to increase the amount of alternative fuel added and reduce the amount of fuel added. Increase coal consumption per unit of clinker and increase production.
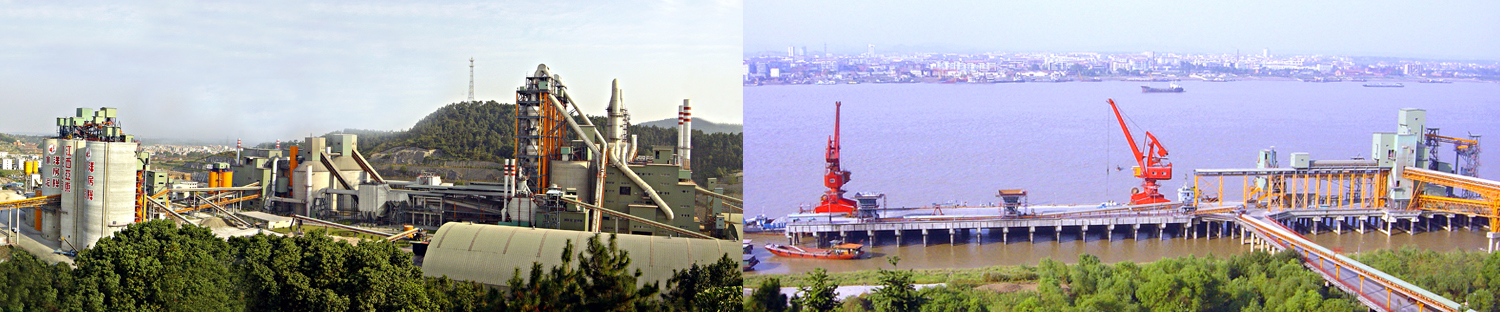
After the addition of a ramp type combustion furnace, the burning condition of the system has changed, and the responsible burners need to adapt again. In addition, as the amount of alternative fuel added increases, the load of the conveying equipment increases, and the structural strength of the original design is also tested; In addition, the impurities contained in alternative fuels can sometimes cause blockage problems; The rapidly increasing demand for alternative fuels also requires teams to replenish their supply in a timely manner... Fortunately, through the collaborative efforts of colleagues from various units, continuous testing and adjustment, difficulties have been gradually eliminated, and benefits have also been gradually demonstrated. Not only has the amount of alternative fuel removed reached 3.4 times before the renovation, effectively saving coal and carbon consumption, but it also assists government agencies and various industries in accelerating the removal of waste or recycled products, increasing the revenue of related treatment fees, and helping to stabilize combustion and reduce air pollution and carbon costs, which can be said to be a win-win situation.
Deepening the cultivation process to achieve increased production and efficiency
If the goal of carbon neutrality is a long-term concern for the cement industry, then the cost increase in the post pandemic era is undoubtedly a near concern. With the combination of energy consumption control and rising coal prices, production costs have been raised and profits have been relatively compressed. For Jiangxi Yadong Cement, in order to avoid affecting operational performance, it is necessary to accelerate the pace of transformation and upgrading. In addition to starting from energy conservation and emission reduction, sand and gravel aggregates with billions of markets are also worth developing.
The bone material production line of Jiangxi Yadong Cement is fed by a limestone crusher combined with a clay crusher. After a comprehensive inspection of the production process parameters by the technical team at the raw material department, it was found that firstly, due to insufficient production capacity during clay crushing, the subsequent vibrating screen machines were unable to feed enough. If the existing 600T/H double rotor clay crusher can be replaced with a 1000T/H single rotor crusher, the production capacity can be increased.
Secondly, after delivery, bone materials still need to be transported to the cabin through belts. However, the loading of bone materials and the limestone required for clinker share the same path. If the loading time of bone materials is increased, the production time of limestone will be shortened, and various units need to cooperate to overcome it. For example, mining a group to assist in improving the production efficiency of the raw ore; The manufacturing team increases the inventory of limestone in the factory to ensure safe production; The port management team needs to improve the efficiency of unloading ships in order to extend the loading time of bone materials. The overall process can be described as interconnected, with one engine pulling the whole body.
In order to be cautious, the project team communicated with the crusher manufacturer multiple times and invited relevant manufacturers to discuss the renovation plan on site. Finally, it was decided to retain the original civil foundation and carry out construction during the shutdown and maintenance period in the factory to avoid affecting the normal production of bone and gravel, and reduce the risk and business losses of project execution.
Despite the tight schedule and heavy tasks, thanks to the careful planning of the mining technical team in the early stage and the close cooperation of the soil, machinery, and electricity units in the process, the equipment update was finally completed on schedule. Unexpectedly, after the increase in production capacity, the particle size of the discharged material was improved, but the problem of high powder material was also discovered. The technical transformation team has made multiple explorations and decided to replace the small belt pulley of the crusher to reduce the linear speed of the rotor and the powder content of the raw ore crushing. As expected, it has successfully increased production and energy, increased the yield of finished products, maximized the utilization of mineral resources, and significantly increased the profitability of the enterprise.
From Asia Cement Corporation in Taiwan to Oriental Petrochemical (Taiwan) cement in Jiangxi, the cement teams on both sides of the Taiwan Strait have deeply explored the production process, identified process bottlenecks, and strived to improve equipment, demonstrating craftsmanship through innovation. This has also helped companies successfully take a big step towards "2050 net zero emissions".
#