2024年05月號 封面故事
创新ⅹ匠心 低碳生产新解方
远东人月刊 / 编辑室採访整理
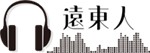
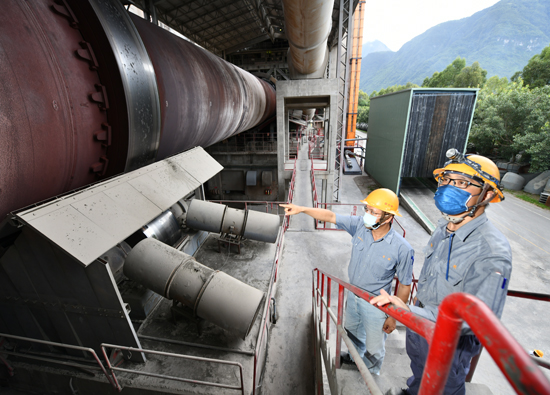
水泥产业的运营除了必须因应矿山石灰石的品质变化,机动调整制程,近年随着环保意识高涨、法规渐趋加严,生产条件更加严峻,唯有加速低碳转型,方有机会突破重围。本期「封面故事」为您介绍集团在两岸的水泥产业如何发挥工匠精神,完成系统改造,朝绿色高效迈进。
研发设备 优化燃料处理
工业革命以来,「原料开採→产品制造→使用→丢弃」的「线性经济」,不仅加速消耗地球资源,也为环境带来冲击,尤其水泥生产模式高度仰赖自然资源,更是屡屡受到环保人士的关注。
另一方面,俄乌战争导致全球燃煤价格飙升、即将开徵的碳费亦造成生产成本急遽增加,如何降低成本也成为各大水泥厂迫在眉睫的挑战。
为了与时俱进,亚洲水泥花莲厂自2019年起,致力朝「循环经济」转型,运作初期是将替代燃料装入太空包,再利用移动式吊车送至预热机6楼,最后以人工破袋方式添加。惟过程中需耗费大量人力、物力及时间,且受限于设备设计,替代燃料的添加量始终有待提升。
2021年建置替代燃料输送设备后,改自专用加料口进料,再以螺运机、提运机及鍊运机等设备,将替代燃料依序分送至各窑,成功提升加料效率。以2号窑为例,平均每月去化量约为人工加料时期的4倍,但碍于替代燃料仍无法完全燃烧,每每提高添加量,即易造成一氧化碳升高、熟料产量降低的问题,因此替代燃料去化量依然面临瓶颈。与此同时,3号窑生料磨的收尘系统由于设备老旧,必须进行为期55天的大修,期间无法协助替代燃料的去化,可能造成堆置空间不足,且无法满足客户需求,如何提升替代燃料的使用量已是刻不容缓。
为此,亚泥花莲厂一方面积极寻求设备商的建议,另方面请制造组、工务组、电仪组团队集思广益,最终决定自力在2号窑增设斜坡式燃烧炉,以加大进料空间,并于底部规划一座小平台,使粒径小的替代燃料可随上升风道直接燃烧,粒径大者则因重力而延长停留时间,待重量变轻时,再被热气带往上升风道燃烧,如此一来,有助于实现完全燃烧,而稳定的热源也将连带使烧成稳定,让烧窑手有空间拉高替代燃料添加量,以降低单位熟料耗煤量并提升产量。
然而,改造的过程并非一帆风顺,举凡斜坡式燃烧炉的造型、内部结构、耐火材料设计,以及各项结构厚度尺寸、是否影响人员动线、加入点温度能否让替代燃料顺利燃烧等问题,都需要团队不断脑力激盪,并藉由现场勘查、实际测量温度、反覆开会讨论才能定案。在各方努力下,顺利趁着2023年4月厂内大修期间建置完成。
新增斜坡式燃烧炉后,系统烧成状况发生变化,负责的烧手皆需重新适应,再者,随着替代燃料添加量提高,输送设备的负荷增加,原始设计的结构强度也受到考验;此外,替代燃料内含的杂物有时容易造成堵料问题;而遽增的替代燃料需求,也需团队及时补充货源…所幸经过各单位同仁通力协作、不断测试磨合与修正,逐步排除困难,也逐渐展现效益,不但替代燃料的去化量达到改造前的3.4倍,有效节省煤炭耗用量,且协助政府机关及各类产业加速去化废弃物或再生产物,亦可增加相关处理费的收益,同时也帮助稳定烧成、降低空污费和碳费,可谓一举数得。
深耕工艺 实现提产增效
如果说碳中和目标是水泥业的远虑,那么,后疫情时代的成本上涨无疑是近忧。随着能耗管控叠加煤炭价格走高,垫高了生产成本,相对压缩了获利,对于江西亚东水泥来说,要避免影响营运绩效,势必得加快转型升级的脚步,除了从节能减排下手,拥有亿万市场的砂石骨料亦是值得开发的领域。
江西亚东水泥的骨材产线是由石灰石破碎机搭配粘土破碎机生产供料,原料处技术团队全面检视生产流程参数后发现,首先,由于粘土破台时产能不足,造成接续的振筛机未能足额进料,若能将现有600T/H双转子粘土破碎机汰换为1000T/H的单转子破碎机,即可提升产量。
其次,提产后,骨材尚需通过皮带才能输送至船舱,惟骨材装船与熟料所需石灰石共用路径,若增加骨材装船时间,则石灰石生产时间变短,需要各单位配合克服,例如,採一组协助提升原矿生产效率;制造组增加厂内石灰石库存,以确保生产无虞;港务组则需提高卸船效率,方能延长骨材装船时间,整体过程可谓环环相扣,牵一髮而动全身。
为求谨慎,专案团队与破碎机生产商多次沟通,并邀请相关厂商到现场共商改造方案,最终决定保留原始的土建基础,并趁着厂内停窑检修期间进行施工,以避免影响骨材碎石的正常生产,降低专案执行的风险与营业损失。
尽管工期紧、任务重,幸赖矿山技术团队前期的精心规划,以及土、机、电各单位在过程中的密切配合,终于如期完成设备更新。不料产能提升后,出料粒径获得改善,却又发现粉料偏高的问题。技术改造小组多方探究,决定更换破碎机小带轮,以降低转子的线速度,减少原矿破碎含粉量,果然成功提产增能、拉高成品率,最大化利用矿产资源,同时也大幅增加企业的盈利。
从台湾的亚洲水泥到江西的亚东水泥,两岸水泥团队深掘生产流程,找出制程瓶颈,锐意精进设备,创新中见匠心,也帮助企业成功向「2050净零排放」跨进一大步。
#