2018年08月號 封面故事
循環經濟發威 水泥業升級綠色產業
遠東人月刊 / 編輯室採訪整理
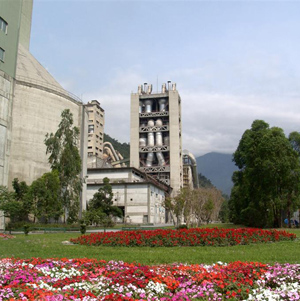
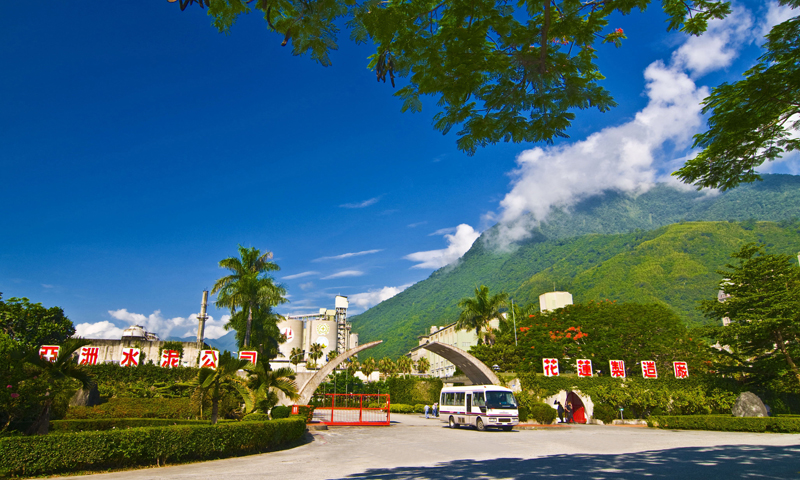
臺灣的垃圾處理以往大多以掩埋為主,隨著經濟起飛,愈來愈多垃圾無處去,1980年即曾發生垃圾大戰,時至今日,垃圾清運仍是許多縣市頭痛的問題。其實,水泥業因製程特性,不僅可有效處理廢棄物,甚至能將廢棄物轉化為替代原料與替代燃料,讓垃圾變黃金。本期「封面故事」特別邀請臺灣亞洲水泥花蓮廠陳志賢副廠長和亞泥(中國)技術部品管及研發處李紹先經理,分享兩岸水泥公司如何成功啟動水泥業的「循環經濟」。
全球吹循環經濟風 水泥業成廢料處理高手
隨著全球環保意識抬頭,「循環經濟」已成為製造業的必修學分,透過重新設計產品和新的商業模式,使廢棄物可再利用,成為良性的資源循環,「水泥業在此模式下大有可為,」亞泥(中國)李紹先經理表示,「因預熱機與旋窯等設備,具有高溫燃燒的密閉環境,可有效消除有害性物質、利用多種工業廢棄物,以及城市生活垃圾、污泥等,在循環經濟中扮演資源綜合利用再循環、再製造的重要角色。」
對此,臺灣亞泥花蓮廠的陳志賢副廠長也十分認同,「臺灣目前來自都會民生及不同產業之廢棄物,除部份回收再利用外,其餘大多採用掩埋或焚化處理,惟現有掩埋場容納量即將用罄,焚化爐處理能量也明顯不足,在社會政治氛圍下,新設掩埋場、焚化爐相當不易,導致全臺垃圾大戰或非法棄置污染的環保事件層出不窮。」更重要的是,焚化或掩埋方式皆可能衍生戴奧辛污染,或後續殘餘灰渣污染地下水問題,「將廢棄物用於水泥製程是更環保的資源再利用方式,可避免二次污染,完全符合循環經濟的概念。」
解決垃圾危機之餘,再利用廢棄物中的成分作為替代原料與替代燃料,更是循環經濟的一大好處,不僅減少原料/燃料開採、降低生產成本,也進一步減少對環境的傷害。因此,李經理深信,「水泥工業循環經濟的推廣,正是將產業由重工業轉型推升為綠色環保產業的契機。」
為促進水泥產業持續發展,美國、日本及歐洲等先進國家都已立法推動循環經濟,李經理指出,「早在1976年,美國即頒佈實施《資源保護回收法》;德國也於1996年制定《循環經濟和廢棄物管理法》;日本則於2000年頒佈《促進建設循環型社會基本法》,其他包括:法國、英國、比利時、澳大利亞、丹麥等國家,自90年代以來,也相繼頒佈實施相關法令。」
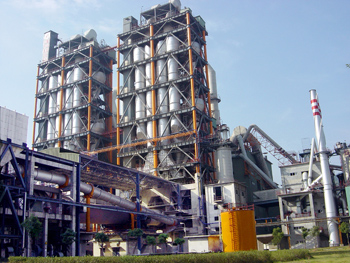
至於產業界也有諸多貢獻,李經理進一步補充,「瑞士霍爾西姆公司(Holcim)在70多個國家設立水泥企業,對於水泥廠處置廢棄物方面有許多值得參考的做法,包括在36個國家建立廢棄物處理中心,並有17座垃圾預處理站,每年可處理約500萬噸廢棄物。無獨有偶,日本三菱材料公司旗下產能最高的九州水泥廠,每天可處置100噸污泥,幾乎能消化掉北九洲下水道的全部污泥,而且九州水泥廠將廢輪胎、廢塑膠、廢燃油和可燃生活垃圾,大量用於生產水泥熟料的燃料,每生產1噸水泥,就可消化431公斤廢棄物和垃圾。至於中國北京的金隅集團公司則於2005年成立北京金隅紅樹林環保技術公司,是大陸地區首家利用水泥窯解決城市環境問題的環保型企業。值得一提的是,北京金隅公司甚至可處理來自工業企業、大專院校實驗室、研究院所的30大類危險廢棄物,尤其還可以處理醫療垃圾,上述廢棄物對水泥窯來說,都不是問題。」
反觀臺灣,根據陳副廠長的觀察,「近年來臺灣水泥廠已陸續使用數種產業廢棄物於水泥生產製程,包括:燃煤火力發電廠之脫硫石膏、飛灰、底灰;水泥旋窯之廢窯磚;電子業之廢溶劑、鋼鐵業之廢爐渣……等。2015年,臺灣水泥業以廢棄物替代原料約115萬噸,替代比率約8.6%;但在替代燃料部份,則幾乎無使用,未來仍有非常大的成長空間。」
變廢為寶 資源再用不浪費
國內外的成功案例,在在證明水泥窯處置廢棄物的可行性,兩岸的亞泥也看準這項趨勢,將循環經濟列為企業發展的一大重點,尤其亞泥花蓮廠早在1990年即投入近2,000萬元設置廢輪胎燃燒設備,希望協助解決廢輪胎去化問題,「不過因工廠位處東部,載運廢棄物的運費極高,造成整體處理成本過高,加上鄰近居民對於燃燒廢輪胎仍有疑慮,計畫因而作罷。」陳副廠長的語氣中難掩遺憾,但亞泥並未就此放棄,而是聚焦替代原料與燃料的使用,包括:利用火力發電廠之脫硫石膏,作為水泥研磨製程之替代原料,或是使用中鋼產生之礦泥,作為生料研磨製程的鐵質替代原料。
2017年6月,臺灣《廢棄物清理法》修法通過,新增「產生廢棄物之事業應與受託處理機構就該廢棄物負連帶清理責任」,此舉也讓廢棄物產出事業更加重視其委託處理的機構能否合法、確實處理。陳副廠長認為,「水泥廠因企業資本額大,具信用可靠優勢,可提升業者合作的意願。」因此,亞泥花蓮廠自2017年起,實地拜訪多種產業,挑選適合導入循環經濟的合作對象,第一階段優先處理縣境內、集團及公用事業產生之廢棄物,來源包括:石材礦泥、淨水污泥、燃煤底灰、焚化再生粒料、消石灰等替代原料,以及漿紙污泥、紡織污泥、廢木材、稻草、RDF等替代燃料。「目前『廢棄物清理計畫書』已完成變更申請,正在申請『固污染源操作許可證』異動,待政府機關核定,即可試車操作,穩定使用後,再進一步申請使用燃煤飛灰、電弧爐煉鋼還原渣、混燒灰、紡織殘料、下水道污泥等替代原、燃料。預計至2020年前,亞泥花蓮廠替代原料使用率可達10%,每年減少開採天然礦物約60萬噸;替代燃料使用率可達7%,每年減少原煤用量約4萬噸,合計每年約可減少10萬噸的二氧化碳排放量。」
場景移到中國,亞泥(中國)對於利用各種廢棄物作為水泥原料也行之有年,包括:鋼鐵公司煉鋼產生的廢棄物「轉爐渣」、「電爐渣」;燃煤電廠排放之「粉煤灰」、「脫硫石膏」、「燃煤爐渣」;有色金屬冶煉廠排放之金屬灰渣;化工廠排放之「硫酸渣」與「磷石膏」,以及金、銅、鐵礦廢棄的尾礦碎屑;石灰石礦山剝離廢棄的高鎂石灰石;碎石場的下角料碎屑與粉末……等,通通可獲得水泥廠有效再利用,且隨著亞泥(中國)生產工藝不斷優化,工業廢渣的利用率也持續提高,李經理統計,「2017年綜合利用各類工業廢渣共計696.86萬噸,成功降低生產成本、節約天然資源耗用,符合政府稅收優惠政策,2017年度本公司退稅金額達6,000多萬元人民幣,進一步提升企業的經濟效益。」
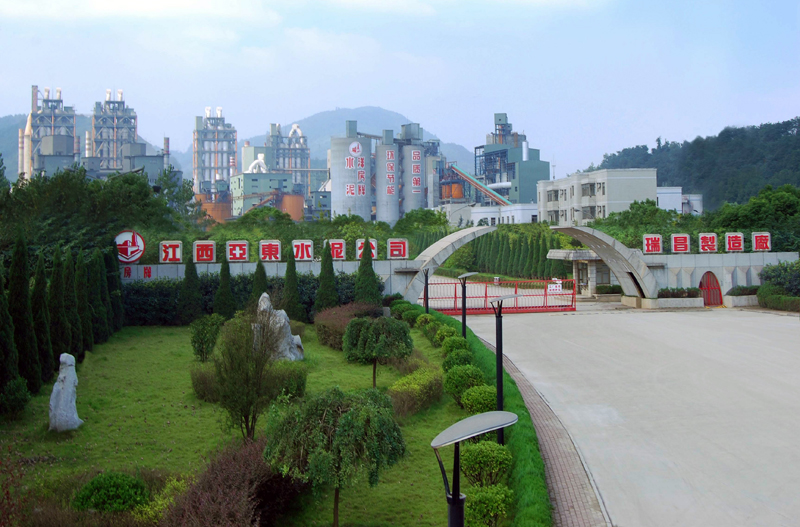
節能減碳 綠色水泥模範生
除了積極發展循環經濟,亞泥多年來也致力節能減碳的各項措施,「花蓮廠自2008年起,幾乎年年進行設備及製程改善專案,以達成溫室氣體減量,合計至2016年,已節省超過2千萬度電、4萬噸煤,CO2減量達16萬噸以上,因此陸續於2009、2011、2013、2015、2016、2017年,獲經濟部工業局頒發『產業自願性溫室氣體排放減量績優廠商』;2017年更認購3.3萬度再生能源憑證,響應政府能源轉型政策。」陳副廠長細數花蓮廠多項減碳作為,同時也預告花蓮廠近期內將繼續執行三號冷卻機熱回收效率改善工程、三號水泥磨排氣風車改善工程,以及四號水泥研磨系統增設三分離式選粉機工程,持續降低生產耗能,朝低碳綠色產業的目標前進。
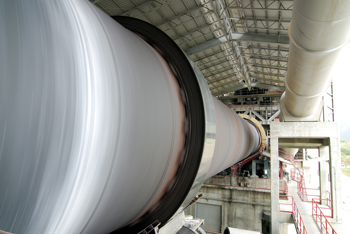
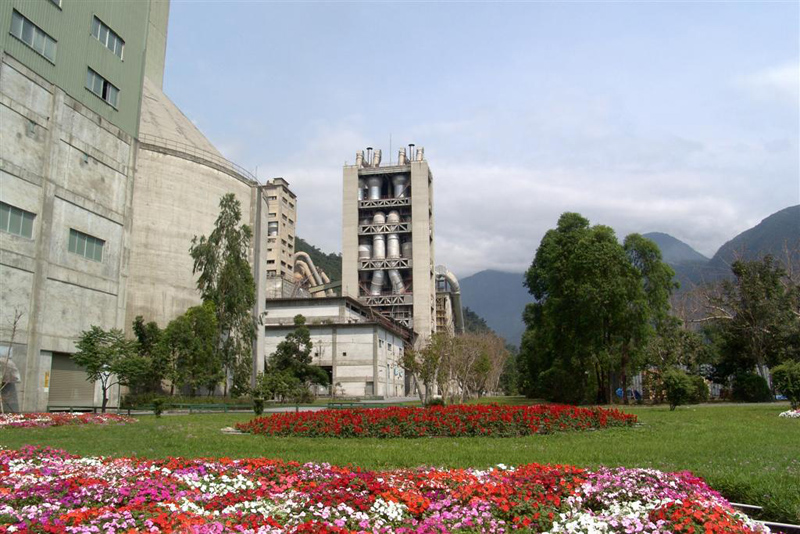