2021年02月號 封面故事
智能煉金術--亞洲水泥點石成金
遠東人月刊 / 編輯室採訪整理
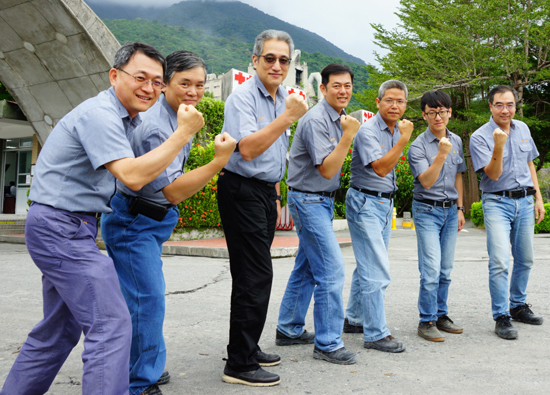
早在4萬多年前,人類已經懂得採掘礦物並運用於生活中。然而各地礦物原料品質不一,加上環保意識抬頭,大面積的隨地開採不僅違背永續精神,同時也有損企業形象。本期將為您介紹亞洲水泥如何在諸多限制下,打造出全新的智慧化生產模式。
緊鄰亞洲水泥花蓮廠的新城山礦場,由於石灰石夾層多且開採面積受限,加上近年來大量矽質、鋁質及鎂質石灰石陸續揭露,使得生產水泥最需要的高鈣石灰石(CaO)嚴重缺乏。不僅如此,花蓮縣政府於民國105年修改地方礦石稅後,花蓮廠每開採1噸石灰石即需繳納高額稅金,不只增加了生產成本,更連帶影響整體獲利。
面對環境與財務上的壓力,花蓮廠專案團隊力求在生產製程面找尋突破點,希望藉由智慧化生產模式,克服天然礦場之劣勢,確保石灰石生產品質,創造更高獲利。
均化措施1:創新開採佈局
俗話說:「知己知彼,百戰百勝。」專案團隊的首要之務是完成礦場全面鑽探作業,以掌握整體礦層走向,了解各類品質礦石之蘊含量及分佈。根據鑽探結果顯示,礦場中的石灰石成分分佈極度不均,且處於高鈣石灰石(CaO)缺乏情況。
為了持續提供符合生產品質之石灰石原料,專案團隊以智慧化模式,建立礦場資源分佈資訊,將人員、機械與礦場資源緊密連結,採特殊模式開採,不但有效掌握石灰石的開採品質,另方面也將礦場石灰石氧化鈣含量最高最低差異從40%之變動,改善至僅有10%。其中非高鈣之低品位石灰石,則透過智慧化調度,直接供應廠內作為生產之副原料使用,大幅降低副原料外購成本。
均化措施2:即時分析及品質監控
除了在開採方法上進行調整,專案團隊積極自法國引進我國水泥業第一套專門分析石灰石的「中子在線分析儀」,每2分鐘可提供一筆分析數據,相較於過往人工取樣分析需耗費60分鐘,時效性提升30倍,且經工程人員測試、改善後,準確度亦有不錯之表現。此外,所有分析數據均透過整合性資訊平臺呈現,使開採單位與品管單位均能即時獲知資訊,並立即進行石灰石品質調度及管控。
此外,團隊也與原廠設備技師共同開發「石灰石下料智慧品質監控系統」,可彈性設定石灰石之品質目標與管制條件,當成分偏離時會自動警報,並預知及因應後續品質調整,不只減少原料的浪費,也提高了石灰石使用效率,使品質可符合生產所用,同時讓進廠石灰石氧化鈣變動由10%,再降至4%。
均化措施3:智慧石灰石堆料模式
根據過往經驗,當礦山石灰石進廠時,由於石灰石顆粒均勻度不同,受到下料堆疊方式影響,料堆兩側容易出現料崩及析離現象,導致堆疊形狀無法匹配刮料機角度,屢屢造成高達16小時以上成分驟變問題,影響後端製程運作。
專案團隊蒐集石灰石堆料機走輪與懸臂高度等資訊,藉由PLC程式進行優化改寫,並重新設計臺車細部設備,打造智慧堆料模式,使料堆堆疊形狀與刮料設備一致,有效提升刮料成分的穩定性,一舉將石灰石氧化鈣變動再優化至2%;同時也解決自開廠以來,料頭料尾石灰石品質差異造成之燒成問題。
均化措施4:自動化配料及精準品質調控
原料配比計算與調整是水泥生料製程中一大關鍵,任何失誤都可能導致品質嚴重失控。為了維持穩定生產,花蓮廠採用自動配料系統進行原料調配。首先,利用實驗室內的半自動研磨製樣系統以及X-ray分析設備,在數分鐘內準確分析樣品的化學成分。配料系統再依據生料品質目標,完成配料計算,並同步透過PLC程式傳遞至現場設備,自動進行秤量機配比調控,以取代過往人工計算並透過聯繫進行配比調整之方式,大幅降低人為誤差,並有效提高生產效率。石灰石氧化鈣的變動也由2%,再降至1%。
亞洲水泥成立六十多年來,無論在研發、品管、工安、環保等面向,始終是我國水泥產業的模範生,本次在專案團隊集思廣益下,推出一系列均化措施,不僅生料品質更加穩定,也降低廠區對於外購原料的依賴,大幅節省營運成本。另一方面,透過智慧化的採礦並配合多樣的植生工法,更加速了礦山景觀回復與水土保持,真正實現永續綠色家園的承諾,堪稱水泥業智慧製造之典範!
#