02.2021 Cover Story
Intelligent alchemy -- Asia Cement Corporation turns stone into gold
Far Eastern Magazine / Editorial Room
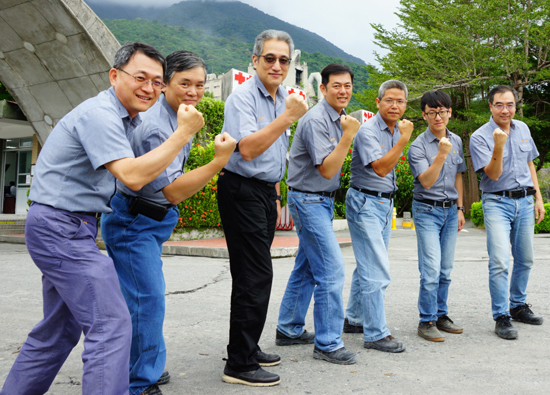
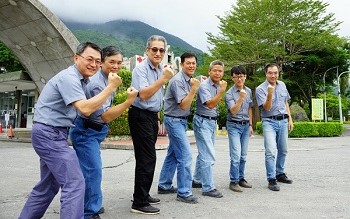
Xinchengshan mine, which is close to Hualien plant of Asia Cement Corporation, is in serious shortage of high calcium limestone (CAO) for cement production due to the large amount of limestone interlayer and limited mining area, as well as the large amount of siliceous, aluminous and magnesian limestone exposed in recent years. Moreover, Hualien County government amended the local ore tax in the Republic of China in 105, and Hualien plant had to pay a high tax for every ton of limestone mined, which not only increased the production cost, but also affected the overall profit.
Homogenization measure 1: innovate mining layout
As the saying goes, "know yourself and the enemy, and win every battle.". The primary task of the project team is to complete the comprehensive drilling operation of the mine, so as to grasp the overall ore bed trend and understand the content and distribution of various quality ores. According to the drilling results, the distribution of limestone composition in the mine is extremely uneven, and high calcium limestone (CAO) is lacking.
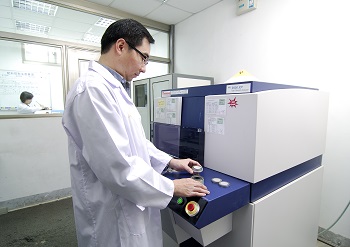
Homogenization measure 2: real time analysis and quality control
In addition to adjusting the mining method, the project team actively imported from France the first set of "neutron on-line analyzer" specially for limestone analysis in China's cement industry, which can provide analysis data every two minutes. Compared with the manual sampling and analysis in the past, it takes 60 minutes, and the timeliness is improved by 30 times. After testing and improvement by engineers, the accuracy also has a good performance. In addition, all the analysis data are presented through the integrated information platform, so that the mining unit and the quality control unit can get the information immediately, and carry out the limestone quality scheduling and control immediately.
Homogenization measure 3: intelligent limestone stacking mode
According to the past experience, when the mine limestone enters the plant, due to the different uniformity of limestone particles and the influence of the stacking mode of blanking, the material collapse and segregation are easy to occur on both sides of the material pile, resulting in the stacking shape unable to match the angle of the scraper, causing the sudden change of composition as high as 16 hours, affecting the back-end process operation.
The project team collected the information of the walking wheel and cantilever height of the limestone stacker, optimized and rewritten the PLC program, redesigned the trolley detail equipment, created the intelligent stacking mode, made the stacking shape of the material stack consistent with the scraping equipment, effectively improved the stability of scraping composition, and optimized the limestone Cao change to 2% at one stroke. At the same time, it also solved the problem of material head loss since the start of the plant The firing problem caused by the quality difference of limestone in the tailings.
Homogenization measure 4: automatic batching and precise quality control
The calculation and adjustment of raw material ratio is one of the key points in the process of cement raw meal production. Any mistake may lead to serious quality out of control. In order to maintain stable production, Hualien plant adopts automatic batching system for raw material allocation. First of all, the semi-automatic grinding sample preparation system and X-ray analysis equipment in the laboratory were used to accurately analyze the chemical composition of samples in a few minutes. The proportioning system completes the proportioning calculation according to the quality target of raw meal, and transmits it to the field equipment through PLC program synchronously, so as to automatically adjust the proportioning of the weighing machine, so as to replace the previous manual calculation and adjust the proportioning through contact, greatly reduce the human error, and effectively improve the production efficiency. The change of limestone calcium oxide also decreased from 2% to 1%.
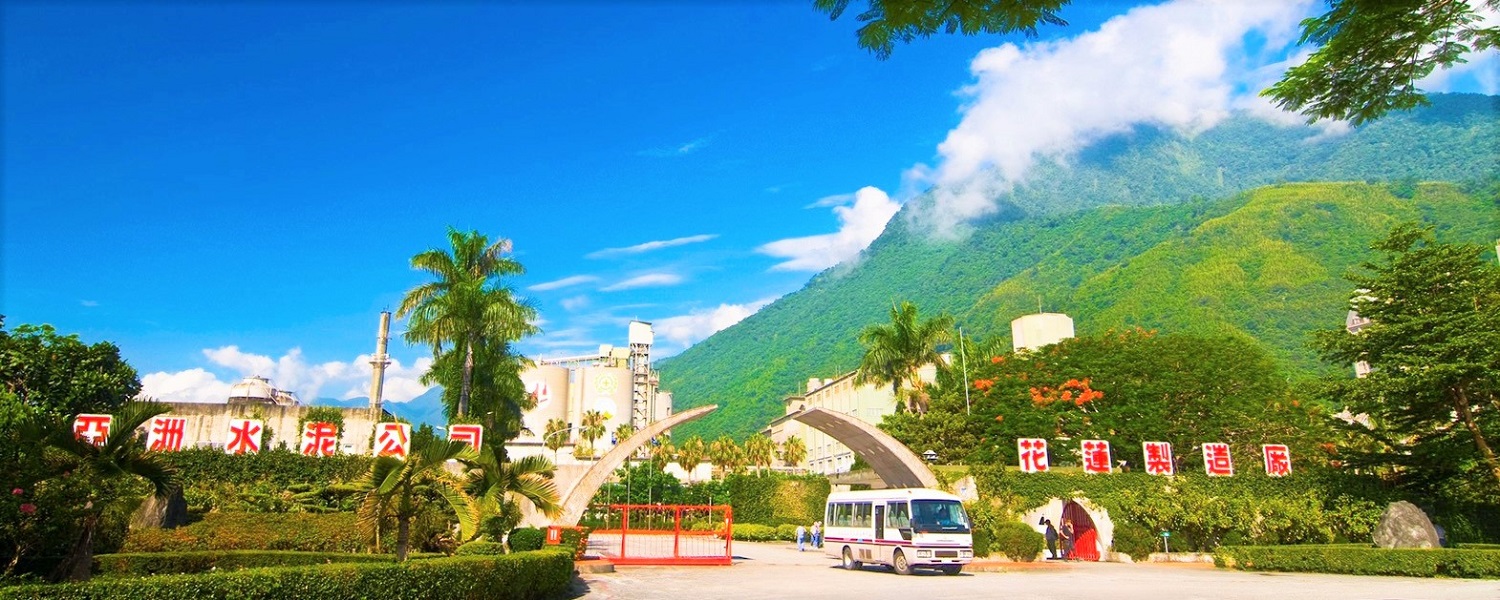
 #