09.2022 Cover Story
Oriental industries (Suzhou) (Suzhou) seizes the opportunity of carbon neutrality
Far Eastern Magazine / Editorial Room
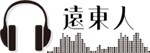
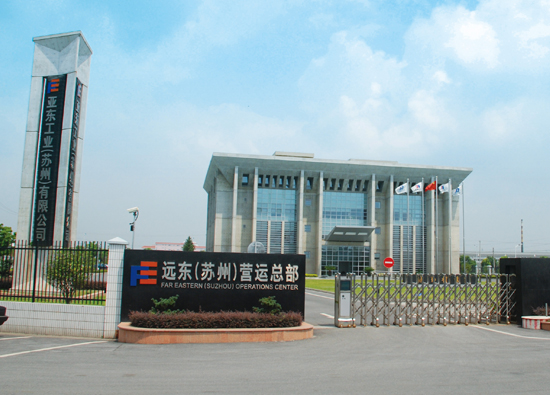
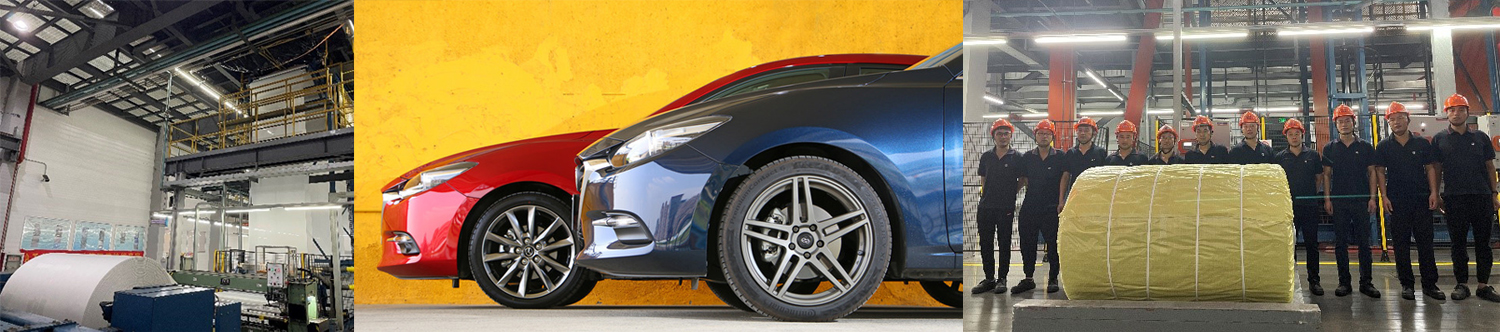
Join hands with brands to enter the electric vehicle supply chain
Pet is not only a common material in daily life, but also often used in the packaging of beverages or snacks, and plays a decisive role in industry. In particular, pet long fiber is widely used in tire cord, vehicle safety belt, airbag, cable wrapping, conveyor belt, etc. because of its high strength and high Danny characteristics, high initial modulus, low elongation and thermal shrinkage, and good impact resistance. Among them, the high modulus and low shrinkage PET industrial yarn has high dimensional stability, constant load elongation, low dry heat shrinkage, and is not easy to deform and shrink due to high temperature. The resulting cord fabric is quite suitable for tire frame materials.
Although cord fabric only accounts for 10% - 15% of tire weight, it accounts for 37% of tire production cost and directly affects tire performance. In particular, in recent years, the world has called for the goal of "net zero carbon emission". The electric vehicle market has rapidly risen. Electric vehicles loaded with battery weight are generally heavier than fuel vehicles, and they need strong, light-weight and energy-saving tire cord fabric.
Although some cord fabric manufacturers in the market have claimed that they can produce relevant goods, they have not been able to produce them on a large scale. Oriental industries (Suzhou) (Suzhou) has long been the carcass cord supplier of Continental, the world's top five tire manufacturers, and its R & D strength has won trust and appreciation. Aiming at the electric vehicle market, after several meetings and discussions, the two sides signed the "JDA cooperative development plan" in 2015, which includes the "development of energy-saving tire cord fabric". They hope to replace the traditional high Danny pet with low Danny pet to produce a new type of tire cord fabric with high strength, high modulus and low shrinkage. Its high strength can reduce the number of layers required for tires, reduce the use of rubber, and achieve the goal of lightweight carcass; The high modulus can improve the dimensional stability of the tire and reduce the rolling resistance; As for the low thermal shrinkage, it can prevent the tire from deforming due to the high temperature of the tread when running at high speed for a long time. In addition to saving energy, it can also improve the comfort, handling and safety of riding.

Generally speaking, after dipping and heat treatment, the strength of high modulus and low shrinkage filaments is in direct proportion to the intermediate elongation and thermal shrinkage. However, the "light-weight and energy-saving high modulus and low shrinkage filaments" required by electric vehicles violate the conventional physical form. It is necessary to reduce the intermediate elongation and thermal shrinkage when increasing the strength. Due to the lack of relevant literature and reference materials, Oriental industries (Suzhou) (Suzhou), under the guidance of the experience of chief operating officer and consultant, tries to readjust the production equipment and process with its own technology combined with the theory of R & D center, including:
1. Redesign the melting parameters of ester particles: ensure that when the viscosity of polymer increases, the flow performance is not affected, and avoid the problem of uneven viscosity.
2. Reform the internal design of the spinning nozzle: prevent the dead angle when the high viscosity polymer flows inside.
3. Test of spinneret aperture and length diameter ratio: avoid wool produced due to abnormal spinning elongation during polymer spinning.
4. Redesign the cooling system: the strength and high thermal stability of the fiber meet the standard by improving the orientation and crystallinity of the fiber.
5. Elongation ratio and temperature test in t / u production drawing process: test the best value to avoid drawing wool due to excessive temperature difference between inner and outer layers of tow.
6. Dipping heat treatment conditions and glue formula: the cord fabric has high strength, fatigue resistance and good high-temperature adhesion.
After 14 months of repeated improvement, testing and tire making verification, the team finally overcame all difficulties and developed a cord fabric whose strength, dry heat shrinkage and constant load elongation reached the expected goals. After being made into a tire, it not only can improve rolling resistance, but also has excellent fatigue resistance and rubber adhesion. It not only successfully obtained the certification of the customer Continental, but also began mass production in 2020, and won patents in various countries. More importantly, The relevant spinning and dipping technologies can also be used to develop other differentiated new products.
As Douglas Hsu said, enterprises must actively predict changes in the market and industry, and formulate new business models and business models as soon as possible. Oriental industries (Suzhou) (Suzhou) has insight into international trends, developed products with unique characteristics and novelty, won the favor of major international manufacturers, and won a place in the electric vehicle market. In the future, with the continuous growth of sales figures of electric vehicles, it will promote the profits of related products and create unlimited business opportunities.
 #