05.2020 Cover Story
Co-prosperity of industry and environment, OUCC turns waste into gold
Far Eastern Magazine / Editorial Room
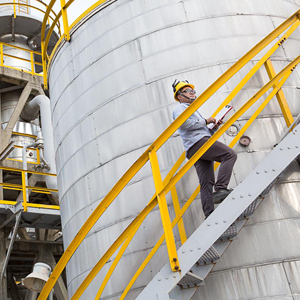
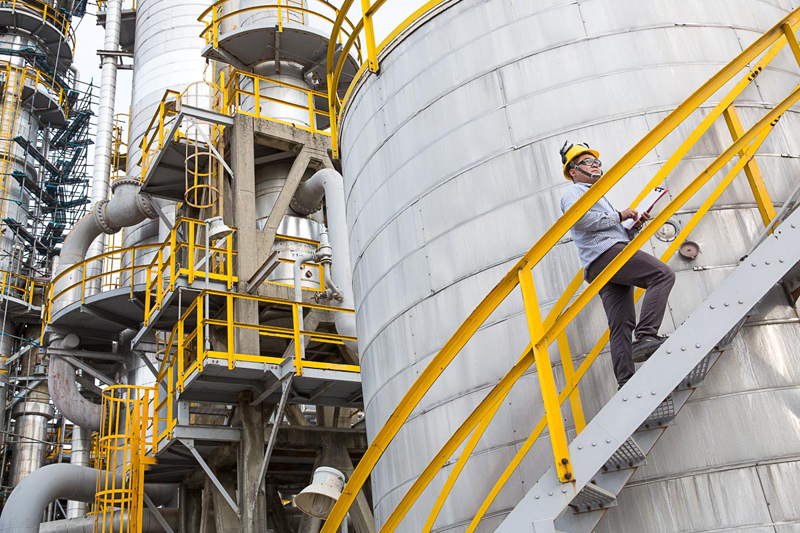
In people's impression, petrochemical industry is always connected with pollution and energy consumption. However, with the more and more severe global climate change, not only the public's awareness of environmental protection is enhancing, but also the industry is committed to reducing the impact of operation on the environment, and seeking more effective use of resources, or even turning waste into energy to reuse resources. This "cover story" specially shares the project achievements of the development of "recycled economy" by Oriental Union Chemical Corporation, let’s see how they can not only implement the environmental protection requirements, but also lead the industrial innovation and transformation.
Turn waste into gold to develop business opportunities
Originally, there was a set of "air separation plant" (hereinafter referred to as "air separation plant") in the Kaohsiung Linyuan factory of Oriental Union Chemical Corporation. In addition to manufacturing oxygen for the production of EG, the remaining gas was purified and then sold to the adjacent factories such as CNPC through pipelines. It is the main industrial gas supplier in the Linyuan Industrial Park. In 2015, in order to meet the oxygen demand of EG capacity expansion, Oriental Union Chemical Corporation added a new set of air separation plant. Because there is no additional gas demand from other factories in the industrial park, the remaining gas in the new air separation plant can only be discharged.
The team of Oriental Union Chemical Corporation learned that the air separation plant of Linyuan plant of Formosa Plastics was about to replace the old one. Based on the principle of perseverance, Linyuan plant of Formosa Plastics was successfully persuaded to cooperate to promote the integration of resources in the Linyuan Industrial Park.
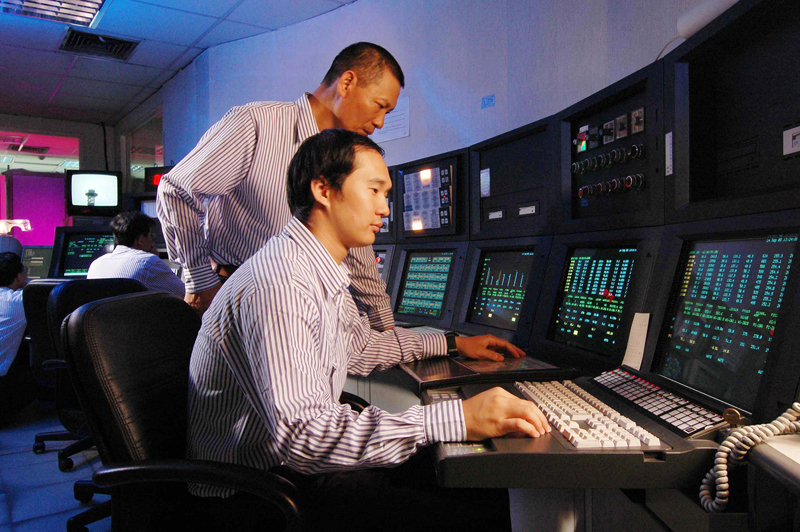
Although it is based on the original intention of mutual benefit and common prosperity, it is not easy to promote. Oriental Union Chemical Corporation team appealed for recycled economy and mutual benefit and win-win situation, and especially emphasized on the stability of supply. It integrated the company's production, technology, maintenance, procurement and other departments, focusing on the pipeline process, backup system, I & C system, pipe and valve design, as well as the time and construction quality of the pipeline laying project inside and outside the plant, meeting the needs of customers and gaining trust, and finally achieving the project objectives, and signing a long-term agreement of gas supply contract with Linyuan plant of Formosa Plastics.
The project was started in February 2017, and gas began to supply in June 2019. The air separation plant of Oriental Union Chemical Corporation gradually reduced the exhaust of residual gas, and relatively increased the effective gas production. The Linyuan plant of Formosa Plastics also significantly reduced the production power consumption, and the gas supply of the production plant was more reliable. The energy conservation and carbon reduction effect of the cooperation between the two sides has become the model of recycled economy in the industrial park.
No waste in production, reuse of waste liquid
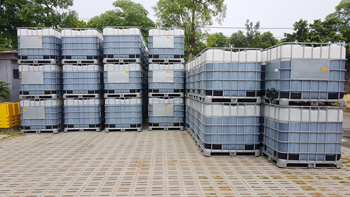
Catalyst of ethylene carbonate (EC) process of Oriental Union Chemical Corporation is discharged with heavy liquid produced by side reaction. The heavy liquid containing catalyst discharged from this similar process was always disposed by a professional waste treatment company, but the heavy liquid containing halogen is not easy to deal with. In addition, the disposal will increase the burden of environment, resulting in the increasing price of outsourcing treatment year by year, and even the professional treatment company will not renew the contract. The topic of heavy liquid containing catalyst will become the hidden danger in developing EC business.
In order to solve this problem, the R & D and technical team of Oriental Union Chemical Corporation developed its own "EC process containing catalyst heavy liquid recovery" technology. Through the hydration reaction and distillation separation process, the concentration of halide in the heavy liquid containing catalyst was successfully increased to meet the allowable concentration conditions of raw materials in foreign catalyst recovery plants, and crude glycol (MEG) could be produced at the same time. Oriental Union Chemical Corporation has obtained the process operation license of "heavy liquid containing catalyst in EC process recovery", and successfully exported the brine by-products after concentration to Japan. The halogen after recycling is made into catalyst, which is supplied to Oriental Union Chemical Corporation for reusing and greatly reducing the cost of catalyst consumption. The other by-product, crude glycol, is refined into polyester glycol product in the EG process of Oriental Union Chemical Corporation, which is a green process technology conforming to zero waste and recycled economy.
It is worth mentioning that the "EC process containing catalyst heavy liquid recovery" process was all developed by the R & D, engineering design and production departments of Oriental Union Chemical Corporation from scratch. During the testing period, in order to overcome the instability of high concentration brine, the project team carried out many discussions and experimental studies, and finally found the most suitable solvent for the concentration process and kept improving. Finally, they developed a unique hydration distillation separation technology, and integrated the EG process in the plant to recycle the crude glycol by-products, so as to surpass the project goal with the minimum investment, the lowest operating cost and zero waste.
Opening the sales channel is another commendable aspect of this project. As the brine by-products after concentration must pass the International ban on waste export transshipment verification, the business team is to clarify the domestic and foreign environmental protection laws and regulations, actively communicate with catalyst recycling manufacturers, arrange sample delivery test, and accumulate many experiences for the overseas supply chain negotiation and production and marketing team cooperation mode of Oriental Union Chemical Corporation.
At present, only Oriental Union Chemical Corporation owns this technology. There is great potential in the future, and it opens a new wave of green business opportunities for enterprises. On the other hand, after the implementation of this case, the benefit of waste reduction reaches 400 tons per year, reducing the environmental burden. With the concept of "resources →products →renewable resources", the "waste" will be turned into gold, which will help to promote recycled economy.
More optimized cooling system for saving electricity
In addition to the use of renewable resources, green environmentally friendly process is also the direction of continuous efforts of manufacturing industry, especially water-saving and power saving not only conform to the trend of environmental protection, but also reduce the operating costs of enterprises. Among them, the cooling water tower is a common heat removal device in the factory, which uses water as coolant to reduce the temperature of the production system. Due to the actual use and heat load of circulating water of No.1 and No.2 cooling water towers in the EOG plant of Oriental Union Chemical Corporation are only 70% - 80% of the design value, the team reconfirmed the cooling water demand of each equipment, optimized the pipeline distribution and adjusted the optimal water supply of each equipment to make more effective use of the equipment.
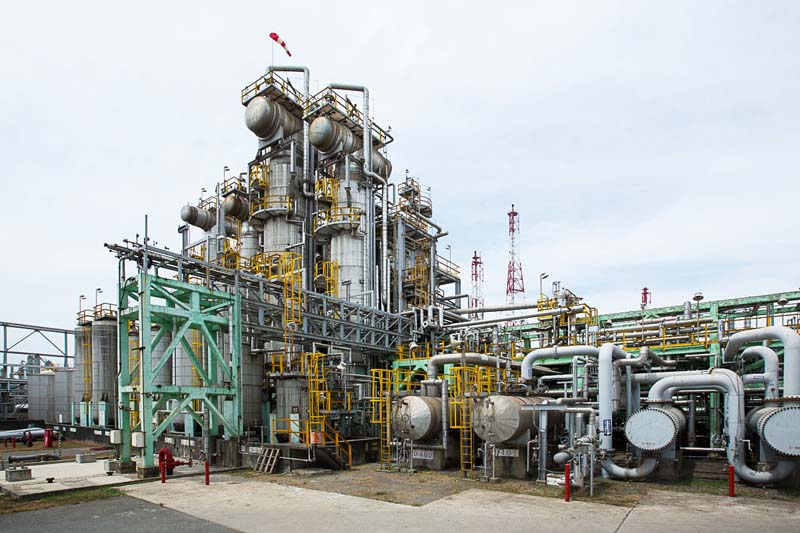
After the implementation of the project, No.1 and No.2 cooling water towers can stop one cooling water pump respectively. Through the DCS (systematic monitoring system) and the newly built "cloud intelligent monitoring system", the adjusted water temperature changes will be continuously monitored and confirmed not to cause harm to the process. The annual power consumption can not only be saved about 6 million Kwh, which is considerable energy cost that is saved, and greenhouse gas emission can be reduced about 3, 174 metric tons. The estimated benefit can last more than 20 years.
This project is introduced by EOG workshop in the Yuanlin plant. Due to the short payback period, innovative and development potential, it will be applied to other production workshops of Oriental Union Chemical Corporation in the future, and even be promoted in other industries, accumulating green energy bit by bit.
Due to its high dependence on natural resources and energy, it is not easy to expand for the petrochemical industry in recent years. In order to reverse the established impression, Oriental Union Chemical Corporation has achieved the goal of zero waste, zero pollution and zero emission by redesigning materials, products, processes and business models, so as to find a new way for the industry and create a new economy that is symbiotic with clients and environment. Wei