07.2020 Cover Story
Initiating the future of AI, OPTC Controls Quality and Energy Consumption Intelligently
Far Eastern Magazine / Editorial Room
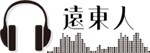
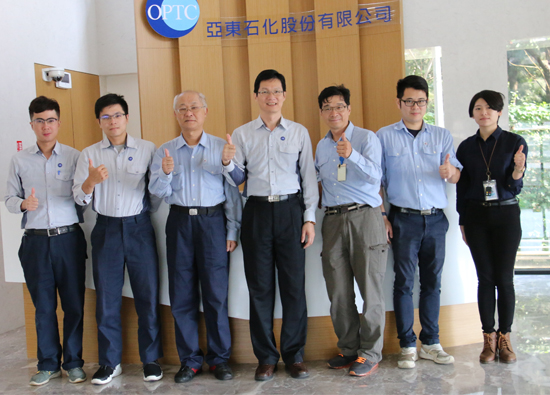
In 2016, the era of vigorous development of Artificial Intelligence (AI) started after AlphaGO defeated the world's Go champion, that made all enterprises actively invested in relevant development and applications. To be in line with the pace of digital transformation of the Group, Kuanyin No.2 plant of Oriental Petrochemical (Taiwan) (OPTC) implemented the industry 4.0 system during the plant establishment. Taking the smart system platform as the core, it extended VR training, smart digital inspection, intelligent logistic management, safety and energy digital dashboard, and monitoring wall system of production site, etc. for a new intelligent chemical plant. OPTC further introduced AI into the process application to make quality prediction and energy management become smarter!
Quality Prediction and Insight into Opportunities
As AI technology is becoming more and more mature, OPTC Technology Department began to introduce AI into the process since 2018, hoping to assist in quality prediction of oxidation process and active energy management of the plant. Because at the early stage of the production, the quality is adjusted according to the results of laboratory analysis. Sampling and analysis are taken at later period during the production. When an exceptional condition occurs, it is impossible to master the quality change immediately. Although the model predictive control (MPC) adopted by OPTC recently helps improving this problem, it is not easy to build and update a traditional model, and it is less accurate in the nonlinear section. If the AI-assisted big data can be used for modelling, the accuracy of quality prediction can be improved further.
On the other hand, most of the energy management methods in the past were adjusted after the event analysis (weekly / monthly review), which resulted in low efficiency. Moreover, the alarm function of DCS (Distribution Control System) could not be used to know whether the energy consumption was abnormal under different refining capacity. Therefore, OPTC hoped that with the help of AI, the change of unit energy consumption can be monitored in real time, so as to make early response and adjustment, keep energy consumption normal and further strengthen energy conservation and carbon emission reduction.
In order to quickly get familiar with machine learning and AI, the project team conducted a preliminary AI modeling evaluation, explored the application of AI with Rapidminer, and conducted AI deep learning modeling and verification. At the beginning, it used the off-line operation mode to collect and process the operation conditions and quality data, and then used DNN (Deep Neural Network) for modeling and testing. For the staff, since AI is a new scientific and technological field, there are many difficulties in the process, such as the adjustment of time difference, the great quality difference between the two production lines, the inconsistency of system data and unreasonable instrument data. Fortunately, after many tests and adjustments, a feasible model of oxidation process quality prediction was obtained and the feasibility of the project was confirmed. For prudence, OPTC invited three suppliers to conduct POC test (proof of concept), and finally selected one to cooperate.
In this project, OPTC provided domain knowledge related to PTA production and assisted in proper data processing, including time differences, outlier data exclusion, etc. Combined with the professional knowledge of PTA and the programming of AI algorithm, a good model was established, and excellent results were obtained in the quality prediction of oxidation process. In addition, compared with the laboratory analysis, the data of AI oxidation quality prediction can be obtained 2-3 hours earlier, so that the staff can adjust the process parameters in advance to stabilize the product quality.
Energy Management and Initiative
The second application to develop by OPTC is the active energy management by using AI technology. This is an innovative idea of the industry. OPTC has approached the Industrial Technology Research Institute (ITRI) for a cooperation project in two stages. At the first stage, a large amount of operation data related to energy was collected and processed properly. Then, the AI energy baseline was established by Rapidminer. After the accuracy of the model is confirmed, the data is transferred to ITRI for AI algorithm coding for establishing AI energy baseline (EBL) model. In the online application, the reasonable unit energy consumption predicted by AI energy baseline model is taken as the standard, and the reasonable range is set as the control boundary, so as to present the trend of energy consumption. When the real-time energy consumption data is beyond the control range, it means that abnormal energy consumption may occur.
It is not enough to find out abnormal condition immediately. Only by finding the cause of the abnormality quickly can we make the management better. Therefore, we have the second stage for developing the function of "automatic search for abnormal energy consumption equipment". OPTC personnel and IRTI experts discussed through each power consumption and power generation equipment, boiler, and heat exchanger, collected and screened data, and then established the reasonable range of feature engineering of each equipment with AI technology and statistical analysis. According to the feature engineering, the data of each equipment under the capacity can be compared in real time. When it is beyond the normal range, the equipment can be regarded as abnormal equipment and the production personnel will be informed right away to correct it.
As a matter of fact, the whole process of AI system construction involves complex cross domain technologies, which must be clarified, communicated and discussed in a multi-faceted and in-depth manner. The project team was not tired of making the system more perfect, which not only made OPTC achieve good results in the field of AI, but also kept the AI program codes and relevant technical information, which means that it has AI technical ability itself. In the future, the program can be extended to high-level process control, optimize operating conditions, and equipment fault warning system, so as to continuously improve production efficiency and reduce operating costs. The first step took by OPTC into AI is expected to be a big step to enhance the company's digital competitiveness.