07.2021 Office Talk
Continuous and stable production of Far Eastern Union Chemical Corporation (Yangzhou)
Far Eastern Union Chemical Corporation (Yangzhou) / Jichun
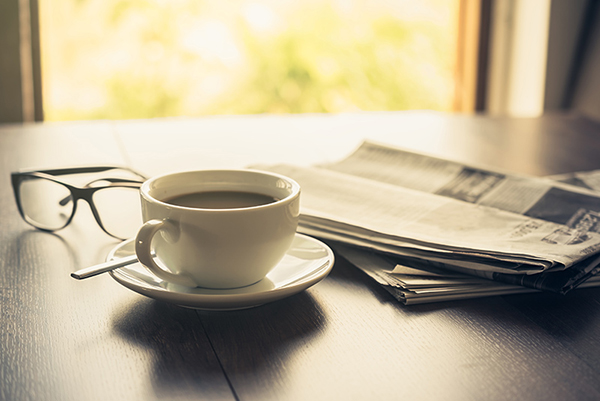
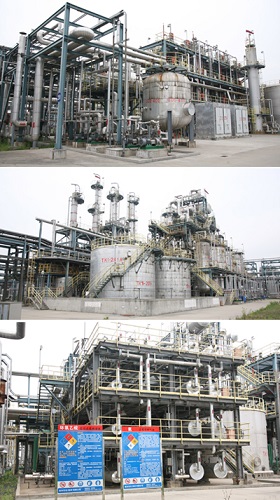
Many people may be unfamiliar with chemical terms such as "ethylene oxide" and "ethylene glycol". In fact, ethylene oxide can be refined into high-purity ethylene oxide, and high-quality ethylene glycol, diethylene glycol and other chemicals can be obtained through chemical reaction. It is widely used in washing and dyeing, electronics, medicine, pesticide, textile, papermaking, automobile, etc Petroleum exploitation and refining and many other fields.
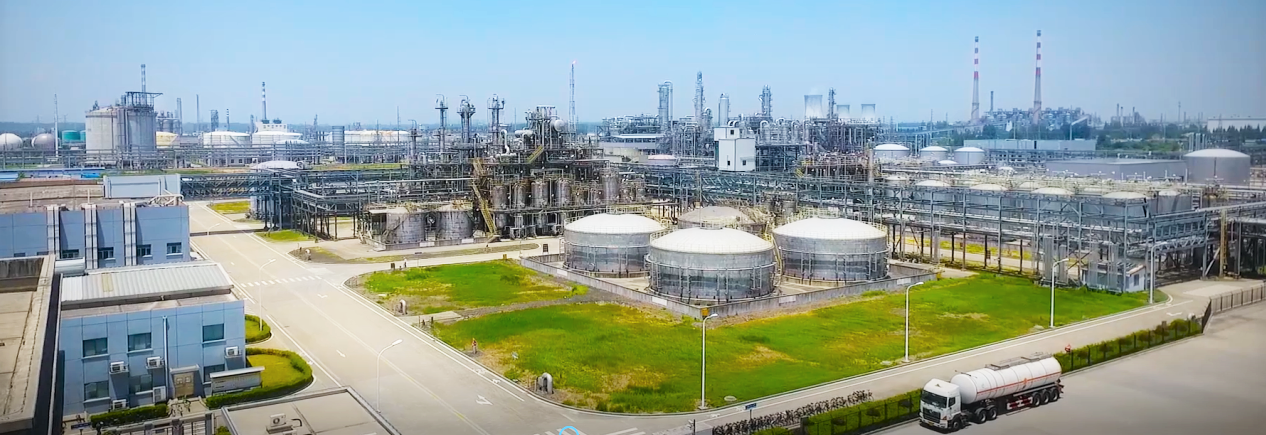
Due to the different basis for each company to calculate the "continuous operation time", even if it is a planned shutdown, the continuous operation time must be reset to zero and recalculated, let alone the successful restart immediately after the shutdown. In addition, ethylene, the main raw material of the plant, as well as a number of important operating units such as power, steam and raw water, are completely dependent on external supply, so the stability of production is easily affected. In addition, limited staffing has set many barriers for this challenge.
Despite this, the operation and maintenance team still adheres to high standards of self requirements, takes the first-class work achievements as the goal, and has the courage to accept challenges.
It's a real skill to be well prepared in the face of danger
The integrity of instruments, machinery and fire-fighting equipment is the basic requirement for the stable operation of production plant. However, even if they are carefully maintained, accidents are inevitable. For example, in November 2020, a small amount of leakage occurred in a control valve, and in February 2021, an internal leakage occurred in a safety valve of a product concentration tower. After the operation and maintenance team finds out the situation, it is not just to eliminate the leakage, but to start to draw up a plan, do a good job in external coordination, manpower and material preparation, at the same time, carry out pre operation safety analysis, and even simulate the maintenance operation in advance. Finally, by reducing the production load, under the condition of absolute safety and ensuring that the device does not stop, the maintenance can be successfully completed and the loss can be avoided.
Although the parts and equipment can be maintained at ordinary times and the value of the interpretation, to predict the situation and solve the problem immediately. However, abrupt weather anomalies, or the development of COVID-19, are not anticipated in advance. At the end of 2020, Yangzhou suffered the most severe cold weather since the plant was built, and the temperature dropped to minus 12 ℃ for several consecutive days. The operation and maintenance team is well aware that many materials in the production plant are easy to freeze due to low temperature environment, which may lead to the distortion of measuring instruments in light cases, and parking or accidents in serious cases. Therefore, it is necessary to check the defects early, make response plans, and arrange the technical backbone to follow the shift, and prepare the repair manpower.
On the night of December 31, 2020, under the temperature of - 8 ℃, the pressure of high-pressure steam drum suddenly distorted, the DCS in the central control room immediately sounded the alarm, and the operators and instrument and electrical personnel on duty immediately rushed to the scene to heat and thaw the pressure pipe with steam. But in the process, another pressure measurement with interlock nearby was also distorted. In just 4 minutes, the pressure rose from 37.5 kgf / cm2 to 49.7 kgf / cm2. Fortunately, the central control room informed the scene with walkie talkie at the first time, heated the steam hose to the interlock pressure measurement point in time, and finally returned to normal. Otherwise, according to the rising trend of pressure at that time, it was calculated, In another 30 seconds, the value will rise to the interlock trip value.
The day after the incident, the team members warmly discussed this soul stirring moment. After all, 12 a.m. is usually a time when people are prone to fatigue. Unless sufficient manpower is arranged in advance to make preparations, give an alarm immediately, and deal with the problem immediately after finding it. In addition, the maintenance personnel are professional enough to correctly judge the cause of instrument distortion in the first time, otherwise it is absolutely impossible to connect 12 10 meter long hoses in a short time to send the steam to the high-rise platform, Finally, it may cause interlock shutdown of the plant, and the process medium in the plant will face the risk of freezing, resulting in dozens of days of shutdown, even affecting the external steam pipe network, and delaying the production progress of other plants.
Strengthen the values of safety production and build an efficient team
Efficient maintenance depends on efficient operation and maintenance team. Looking back at the initial stage of the plant, the staff came from all over the world and all enterprise platforms. In order to avoid colleagues being afraid of trouble or thinking that it was just a small matter and unwilling to report, the company implemented the exemption report system to encourage everyone to report honestly, find out the causes and eliminate hidden dangers fundamentally. Respect and trust bring honesty and openness, and at the same time greatly reduce the cost of communication. Nowadays, even if team members occasionally slip up and down the stairs, they will take the initiative to be included in the review of accident management, hoping to create a better working environment.
In addition, in order to do a good job in the basic work of plant production, the operation and maintenance team not only formulates and strictly implements the standard operation manual for parking, unit operation, emergency treatment, important equipment operation, major hazard inspection, central control room operation, inspection and maintenance, etc., but also often through pairing training, simulation operation training, rolling rotation training according to training topics and other activities, Cultivate the values of safety work. What we often hear in our production line is: safety work is always on the road, no work is so important that it can't be carried out safely, and safety work is the most efficient!
Looking forward to the domestic petrochemical industry environment, many newly established large-scale petrochemical projects actively attract talents. Although the flow of talents is a good thing from the perspective of the whole society, it still has a great impact on the stable production of individual plants and single units. On the other hand, the continuous chemical safety accidents such as the "3.21 particularly serious explosion of Xiangshui tianjiayi chemical industry in 2019" lead to the color change of people talking about chemical industry. In addition, due to the strict production conditions of chemical industry and the time-consuming and painstaking study of related majors, talent recruitment has become a common problem faced by the chemical industry. In addition to theoretical study, on-site practice training is more important and needs long-term training to meet the requirements of production posts. Fortunately, Far Eastern Group has excellent corporate culture, rigorous system and process. As long as we continue to strengthen skill training, gather safety work values, establish environmental protection and energy conservation awareness, and actively seek artificial intelligence empowerment, we believe that we can not only achieve the goal of safe production, It will also strive for better results for Far Eastern Union Chemical Corporation Petrochemical (Yangzhou) Co., Ltd!
* Note: by the deadline of June 15, the ethylene oxide / glycol production line of Far Eastern Union Chemical Corporation (Yangzhou) had been "continuous and stable production" for more than 300 days.
 #