03.2019 Cover Story
Green Pioneer of Petrochemical Industry,Oriental Petrochemical (Shanghai) Corporation Converts Waste to Energy
Far Eastern Magazine / Editorial Room
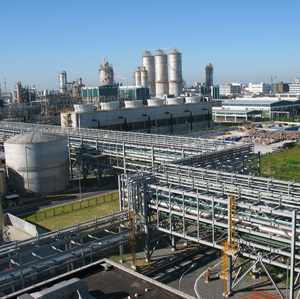
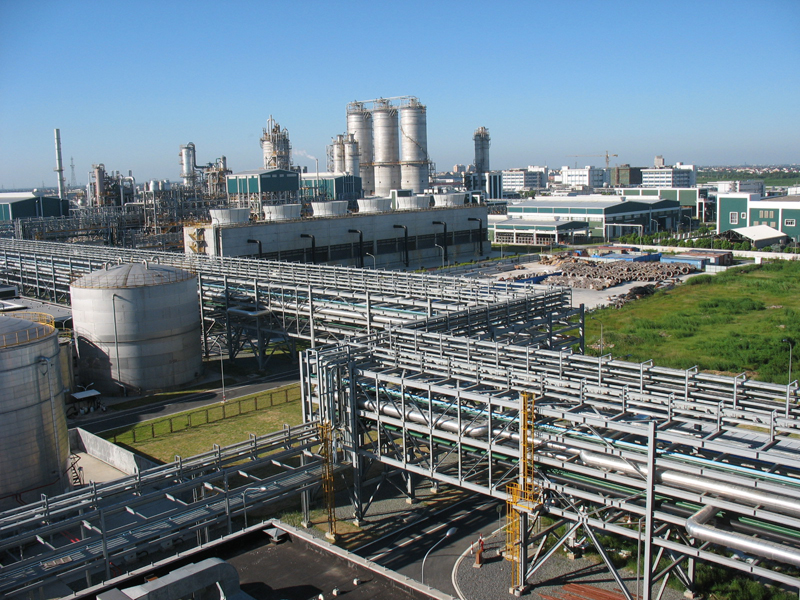
With the rise of global awareness of environmental protection, recycled economy, which aims at "zero waste", has gradually become a prominent learning. Among them, "resource reuse" is the most common and basic effort. However, for Oriental Petrochemical (Shanghai), resources are not limited to the original materials, and even the waste produced in the process can be transformed to create new prices. Value. This issue of "Cover Story" will introduce how Oriental Petrochemical (Taiwan) (Shanghai) put forward new ideas for energy saving and carbon reduction through its original tail gas recovery method.
Process review and implementation of green management
Far Eastern Group, for example, is best known for its environmental protection yarn Jersey made from recycled jewelry bottles and its appearance in international competitions, making it an alternative Taiwanese light. Cement industry has a closed-loop environment of high temperature combustion. It can effectively deal with domestic waste, sludge and industrial waste, and waste can also be used as alternative raw material or fuel in cement production process. It is an important industry to promote recycled economy development. As for Oriental Petrochemical (Shanghai), which is also a manufacturing industry, in order to achieve the Sustainability Development goal, we are constantly thinking about improvement plans from the process. Among them, the "Rotary Pressure Filter System Exhaust Gas Recovery Project" not only conforms to the trend of energy saving and carbon reduction, but also is an innovative application of recycled economy.
The so-called "tail gas" is actually the waste gas produced in the process. Although it is waste, the industry and academia have invested in the technology research and development of secondary utilization. Before the system reform, the Oriental Petrochemical (Taiwan) (Shanghai) pressure filter (RPF) directly discharged the exhaust gas into the atmosphere like other factories, without recycling. Because of the large volume of air and the pressure of about 3barg, the noise on site was very high. Another equipment, oxidation dryer, needs to use a large amount of air-driven tail gas to transport dried products (powder). Air-driven tail gas usually comes from 7.5 barg of high-pressure tail gas through pressure relief valve. Because the air-driven pressure of powder is low (about 1 barg), it makes 3 barg of exhaust gas useful after recovery. The project team therefore considered that if RPF waste exhaust gas could be supplied to the air supply system of oxidation dryer, it would save a lot of original exhaust gas consumption, save high-pressure exhaust gas could be fed into expander to generate more electricity, reduce costs and reduce waste of resources.
In fact, the exhaust gas reuse of pressure filters in PTA plant is not a new thing. All other factories recycle by compressors, but this method is not adopted by Oriental Petrochemical (Taiwan) because of its high power consumption and poor economy. After team research, we decided to adopt innovative recycling methods to recycle the exhaust gas to the air supply system of oxidation dryer, save the original exhaust gas consumption, increase power generation, and solve the noise problem at the same time.
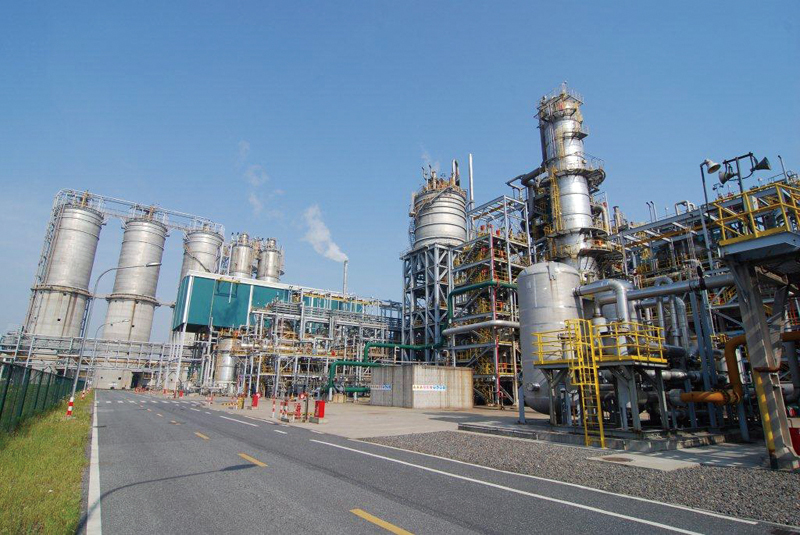
The project team thought of adding a set of tail gas dewatering and purification devices after the pressure filter (RPF) system, so that the pressurized tail gas from the RPF high-pressure tail gas scrubbing tower can be sequentially entered into the cooler and the dry cooler, and the cooling, condensing and dewatering procedures can be carried out, and then dried into the adsorption tower to meet the dew point requirements. Generally speaking, the lower the dew point, the smaller the moisture content, the better the drying effect. At this stage, Oriental Petrochemical (Taiwan) (Shanghai) specially set up two adsorption towers to ensure the continuous adsorption process. The tail gas from the adsorption tower is filtered through the product gas filter and then sent to the air supply system of the oxidation dryer, which can replace part of the original tail gas. The saved tail gas is directly fed to the expander to generate electricity, thus completing the recovery process.
According to the statistics of the project team, the consumption of air supply tail gas of the reformed oxidizing dryer has saved 4 tons/hour compared with the previous one. According to the calculation of 8000 hours of operation and 318.6 yuan (NT$) of one ton of power generation from tail gas, the electricity cost saved in the whole year exceeds 10 million yuan (NT$) and about 9 million yuan (NT$) of electricity can be saved after deducting the operation cost.
This way of saving exhaust gas, increasing power generation and reducing noise at the same time has not been used by other factories at present. It can be regarded as a lone step in the industry. It is expected that the national invention patent will be obtained in two years. What's more, all high-pressure exhaust gas systems, as long as the pressure is appropriate, can learn from this technology to recover, provide air distribution system reuse, and have full potential for promotion.
Petrochemical industry belongs to high energy-consuming industry. In the environment of high environmental awareness and lack of electricity, the demand for energy conservation and carbon reduction is more intense. The success of Oriental Petrochemical (Taiwan) (Shanghai) project on tail gas recovery of rotary pressure filter system undoubtedly drives the green management of industry forward, and opens up the opportunity of recycled economy, expecting to pass through more in the future. Innovative technology, turn over the industrial constitution, create lasting value.