03.2019 Cover Story
Asia Cement Corporation, an excellent student of energy saving and carbon reduction, realizes its dream of environmental protection by means of Technology
Far Eastern Magazine / Editorial Room
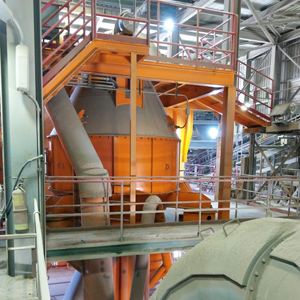
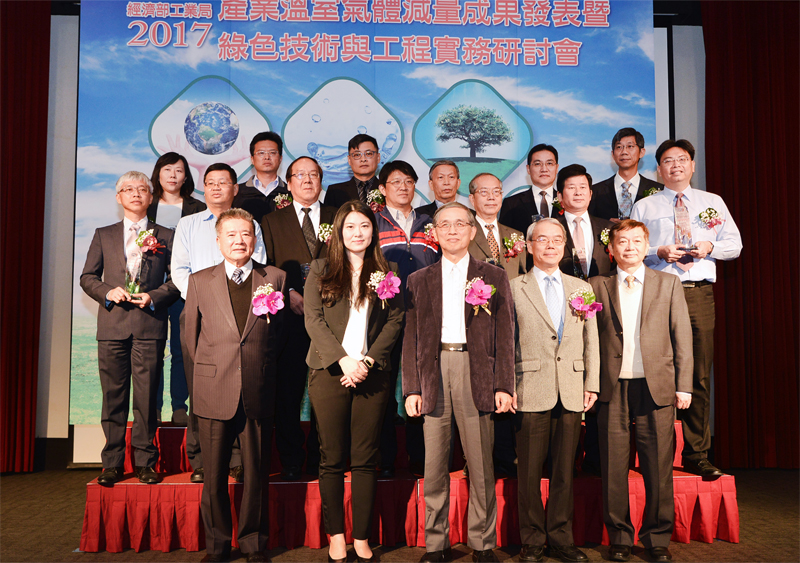
Cement industry is the foundation of people's livelihood and national defense, but in the manufacturing process, it is inevitable to consume a lot of energy and emit considerable greenhouse gases. In order to reduce the impact of industry on the environment, Asia Cement Corporation has been committed to energy saving and carbon reduction in all aspects of process and products for a long time, with excellent results. Hualien has won the "Greenhouse Gas Reduction Excellent Factory" Award for six times. It is not only the most important factory in the whole plant, but also creates new possibilities for the harmony of industry and environment.
Intensive development process to improve energy efficiency in all directions
Cement manufacturing process must consume a large amount of fuel and electricity, with an average of about 140 kg of coal and 100 kW of electricity per tonne of cement production. These energy consumption will directly or indirectly emit greenhouse gases, together with the main raw material limestone, which will generate carbon dioxide in the process of forging, resulting in about 0.82 tonnes of greenhouse gases per tonne of cement production, and the construction of the environment. As a result, Asia Cement Corporation has made great efforts to realize the Sustainability Development of industry and environment.
Since 2009, the Asian Cement Corporation Hualien Factory has joined the ranks of "Voluntary Reduction of Industrial Greenhouse Gas" promoted by the Ministry of Economy. As of 2017, it has won six awards for "Voluntary Reduction of Industrial Greenhouse Gas Excellent Performance Manufacturers". The awards are not only the first in the cement industry, but also the only and six-time award-winning factory in the 245 voluntary reduction factories. Investment and leadership in process improvement, energy efficiency improvement and innovative products.
In terms of process improvement, Asia Cement Corporation has been promoting various measures for many years, such as updating the main motor to increase rotary kiln speed, thereby reducing clinker burning heat consumption by using thin fast burning technology; furthermore, promoting the revision of CNS national standard and adding a small amount of limestone in cement grinding process to reduce clinker usage, which not only conforms to the world standard trend, but also can simultaneously. Considering the quality of cement, the greenhouse gas emission per ton of cement has been reduced by 3%, leading the industry to follow suit.
Not only that, the waste heat recovery power generation initiated by Asia Cement Corporation can recover up to 30% of the total plant power consumption. The use of V-type high efficiency flour separator and raw material grinding dust collector windmill instead of DC motor in cement grinding also has the substantial effect of reducing greenhouse gas emissions. In recent years, more than Taiwan's counterparts, coolers have changed to the latest push stick type fixed grate to improve heat recovery efficiency, greenhouse gas reduction can reach 1.8% of the total emissions; in addition, in order to increase the length of the riser duct of the preheater, increase pulverized coal combustion time, improve combustion efficiency and reduce coal consumption... Various energy-saving technologies have accumulated the environmental benefits of Asia Cement Corporation bit by bit.

Innovative Idea of Optimizing Equipment Power Saving and Increasing Production
Particularly noteworthy is the "Energy-saving Optimizing Improvement Plan for No. 4 Cement Mill of Hualian Plant", awarded by the Industrial Bureau of the Ministry of Economy in November 2017, which effectively improves and improves the grinding efficiency of the ball mill through the combined dynamic and static three-phase separator system, thus achieving the effect of increasing production and saving electricity.
After CKP vertical grinding of existing main equipment, a new combined dynamic and static flour separator is added in this project. When clinker, gypsum and limestone are vertically grinded by CKP, the combined dynamic and static flour separator can carry out primary selection and divide the material into three parts: coarse, medium and fine. Among them, coarse-grained materials return to CKP vertical mill and continue to crush; medium-grained materials are sent to subsequent ball mill for grinding; and the finest powder is collected by cyclone, and directly into the finished product delivery system, thereby excluding large-grained materials into the ball mill, affecting grinding efficiency, while avoiding excessive fine powder back to CKP vertical mill, waste of work.
After modification of equipment, the particle composition of materials entering ball mill has changed greatly, which results in the change of operation conditions and parameters of the original system. After many discussions and studies, the project team actively adjusts the ball ratio of the mill, improves the wear resistance of the components in the oblique groove and wearable parts, and optimizes the main process equipment, so as to rationalize the operation parameters and make them more reasonable. The product achieves the ideal quality.
Moreover, in order to accomplish the task with the least investment, the project team carefully considers the cost of the earth construction, and must complete all the projects in the existing plant in order to reduce the cost; and in order not to affect the operation of existing production equipment, the combined dynamic and static three-phase separator, system circulating fan, cyclone and conveying equipment added in the project must also be in the shortest possible time. The transition was completed in time. Fortunately, through the efforts of the team, the challenges were overcome one by one.
The success of this project will undoubtedly add another momentum to the energy saving and carbon reduction of Asia Cement Corporation, which will not only reduce power consumption by more than 10%, but also reduce greenhouse gases by 55,840 tons over the next 20 years. In addition to the substantial benefits, this project is also the latest initiative of Taiwan's cement industry. The team was even invited to conduct a "Demonstration of Low Carbon Green Processing Technology in Cement Industry" commissioned by the Industrial Bureau of the Ministry of Economy in 2017, leading the industry to observe on-site, not only to enhance the green image of enterprises, but also to spread the application of low carbon technology in the cement industry.
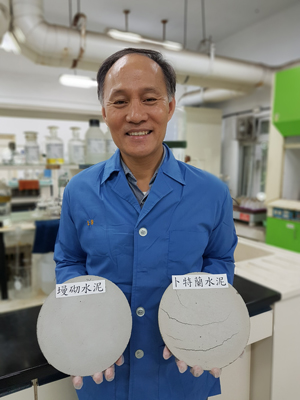
In addition to process improvement and efficiency improvement, Asia Cement Corporation also aims at environmental protection in product development. The cement developed by Hualien Plant can reduce 7% natural minerals and 17% coal consumption in the production process, and has high crack resistance. It can effectively reduce cracking problems and improve the quality of mud works. It has gradually become the preferred material for environmental protection, energy saving and quality assurance in the decoration industry. Compared with the common Putland cement on the market, the cement can save 16% of greenhouse gas emissions. All bagged cement can be replaced by batch cement, which can reduce greenhouse gas emissions up to 264,000 tons per year, equivalent to the carbon adsorption capacity of 679 Taipei Da'an Forest Park, with considerable results. Hualien is the only factory in Taiwan that produces and sells bathroom cement.
With long-term efforts, the energy-saving and carbon-reducing work of Hualien Plant of Asia Cement Corporation has accumulated considerable benefits. The greenhouse gas reduction measures recognized by the Industrial Bureau can save 139 million degrees of electricity per year (equivalent to 33,000 household electricity), 42,955 tons of coal and 298 tons of fuel oil, and 267,345 tons of carbon dioxide emissions per year. In addition to the technology of greenhouse gas reduction, Hualien has spared no effort to promote environmental education, build butterfly and bamboo insect parks, and mine planting and greening, soil and water conservation and blasting control technology. Hualien has the world's proud achievements.
Looking forward to the future, Asia Cement Corporation will cooperate with the government to promote the policy of "recycled economy", referring to the "Cement Technology Roadmap" published by the World Business Sustainability Development Association (WBCSD), plan Hualien plant to reduce carbon as a substitute for some natural raw materials and fossil fuels by using waste and its derivatives. Progress and active action are expected to produce considerable energy saving and emission reduction benefits.
The International Cement Sustainability Development Initiative points out that the cement industry still has the potential to reduce greenhouse gas emissions substantially, and technology is the key to reducing emissions and energy consumption. Innovation motivation, conceive how to continue to pay a brilliant report card. Under this belief, Hualien plant's production, engineering, environmental protection and quality control units are united in consensus and strength, striving for excellence year by year on the road to energy conservation and carbon reduction, and continuing to practice the concept of "industrial development and environmental protection go hand in hand".